Welcome busy families! Are you looking for a time-saving solution in the kitchen? Speed up meal preparation with the Maytag Gas Range with Speed Cook Microwave! With its exceptional features and convenient design, this appliance is perfect for families on the go.
Handling the Hassle of Hectic Schedules
Balancing work, family, and other commitments often leaves limited time for cooking. Traditional meal preparation methods can be time-consuming, adding stress to already busy schedules.
The Savior in the Kitchen: Maytag Gas Range with Speed Cook Microwave
The Maytag Gas Range with Speed Cook Microwave is the solution for busy families. It seamlessly combines a gas cooktop with a built-in microwave, allowing for the preparation of multiple dishes at once, saving valuable time.
Key Features of Maytag Gas Range with Speed Cook Microwave
The Maytag Gas Range with Speed Cook Microwave boasts a range of features that enhance convenience and efficiency:
- Speed Cook Microwave: Quickly heat or cook small portions, ensuring a fast and fuss-free experience.
- Powerful Gas Burners: Deliver precise heat control for optimal cooking results.
- Spacious Cooking Surface: Provides ample space for multiple pans and pots, accommodating family-sized meals.
- Easy Clean Design: Its smooth surfaces and removable parts simplify cleaning, saving you time and effort.
Personal Experience with the Maytag Gas Range with Speed Cook Microwave
As a parent with a busy schedule, finding time to cook healthy meals for my family was a constant struggle. The Maytag Gas Range with Speed Cook Microwave has been a game-changer in my kitchen.
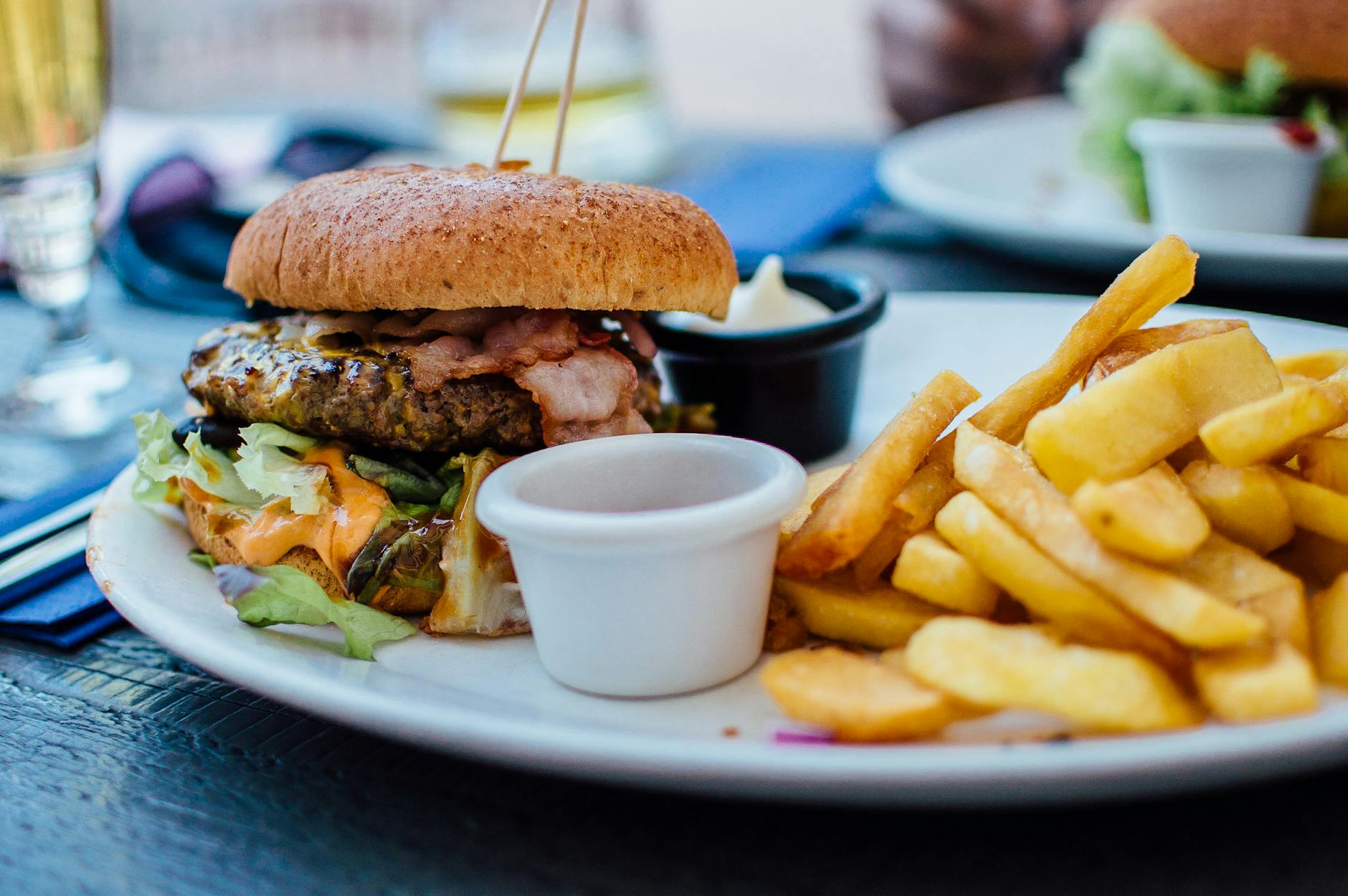
With its powerful burners, I can sauté vegetables and sear meat effortlessly. The Speed Cook Microwave is a lifesaver for quickly reheating leftovers or preparing side dishes. The large cooking surface allows me to cook multiple dishes simultaneously, which is a huge time saver.
The History and Innovation of Maytag Gas Range with Speed Cook Microwave
The Maytag Gas Range with Speed Cook Microwave is a testament to Maytag’s commitment to innovation and customer satisfaction.
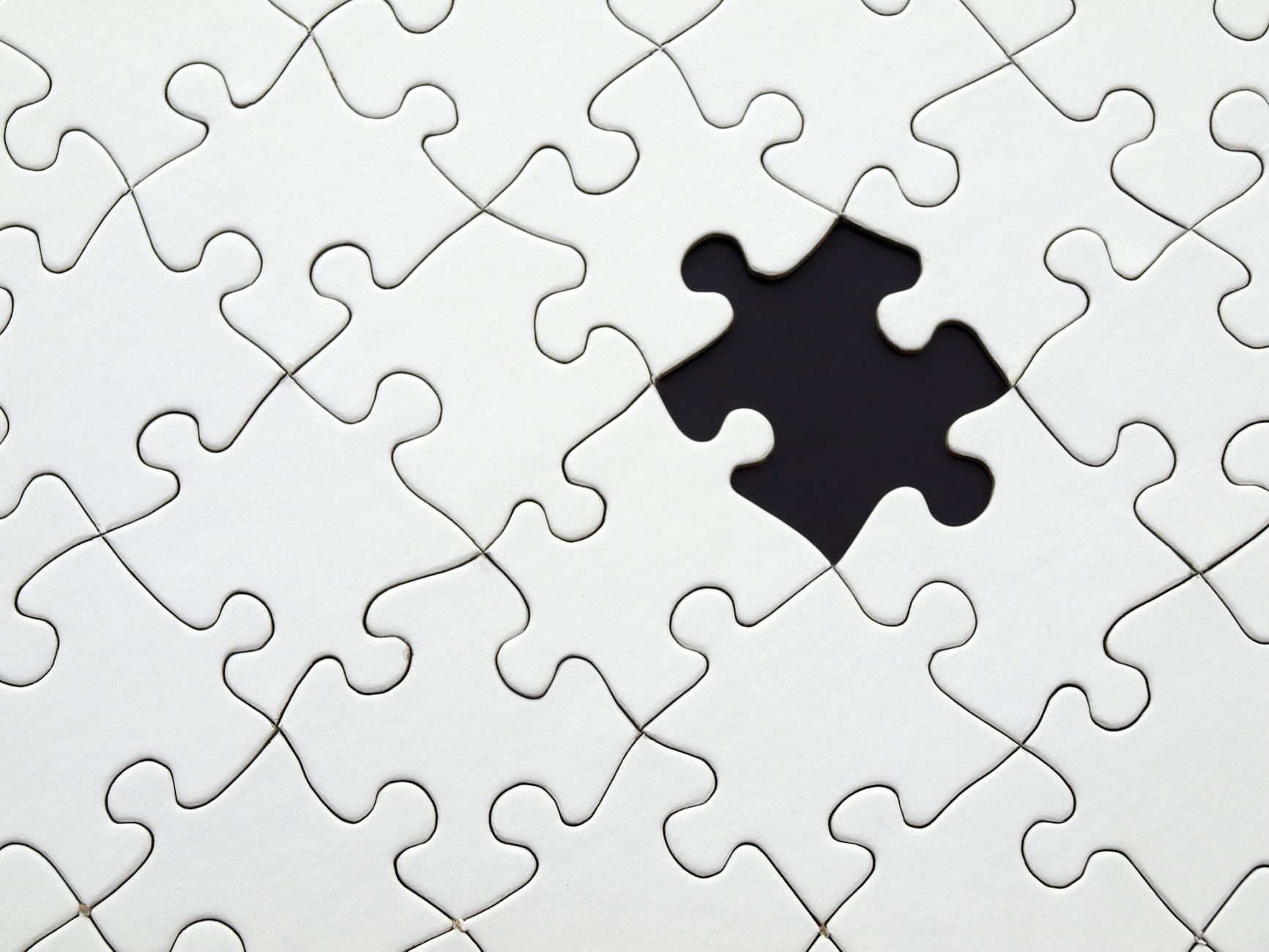
Over the years, Maytag has consistently pushed the boundaries of kitchen appliance technology, with the Speed Cook Microwave being a prime example. This innovative feature combines the convenience of a microwave with the precision of gas cooking.
Unveiling the Hidden Secrets of Maytag Gas Range with Speed Cook Microwave
Beyond its exceptional features, the Maytag Gas Range with Speed Cook Microwave holds a few hidden secrets that enhance its usability.

The intuitive control panel allows for quick selection of cooking settings and easy adjustment of time and temperature. Additionally, the appliance features a built-in timer to prevent overcooking.
Recommendation for Families with Hectic Schedules
The Maytag Gas Range with Speed Cook Microwave is highly recommended for families with busy lifestyles, providing the following benefits:
- Time-saving: Prepare multiple dishes simultaneously, reducing overall cooking time.
- Convenience: Combine the benefits of a gas cooktop with a built-in microwave in one appliance.
- Efficiency: Powerful burners and a spacious cooking surface ensure efficient use of space and energy.
- Easy maintenance: Smooth surfaces and removable parts make cleaning a breeze.
Maytag Gas Range with Speed Cook Microwave: A Smart Investment
The Maytag Gas Range with Speed Cook Microwave is not just an appliance; it’s a smart investment that saves you time, simplifies cooking, and enhances the quality of family meals.
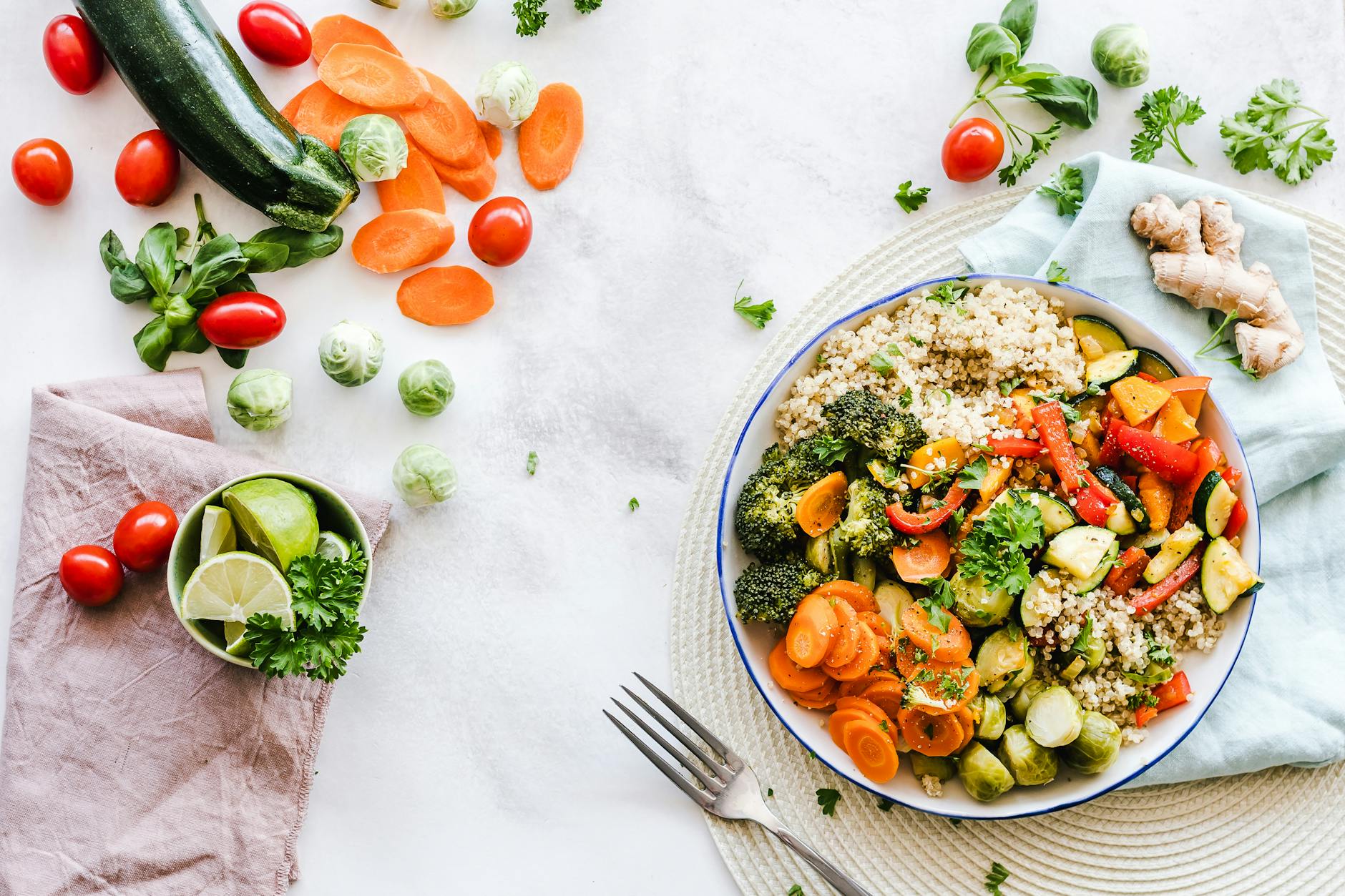
Its combination of speed, convenience, and efficiency makes it an indispensable kitchen companion for busy families. Invest in the Maytag Gas Range with Speed Cook Microwave today and experience a transformed cooking experience.
Tips for Utilizing the Maytag Gas Range with Speed Cook Microwave
Make the most of your Maytag Gas Range with Speed Cook Microwave with these tips:
- Use the microwave for quick reheating of small portions or defrosting frozen foods.
- Experiment with the Speed Cook Microwave settings to find the optimal cooking times for your favorite dishes.
- Take advantage of the spacious cooking surface to prepare multiple dishes simultaneously, saving time and energy.
- Keep the appliance clean to ensure optimal performance and extend its lifespan.
Fun Facts about Maytag Gas Range with Speed Cook Microwave
Did you know these fun facts about the Maytag Gas Range with Speed Cook Microwave?
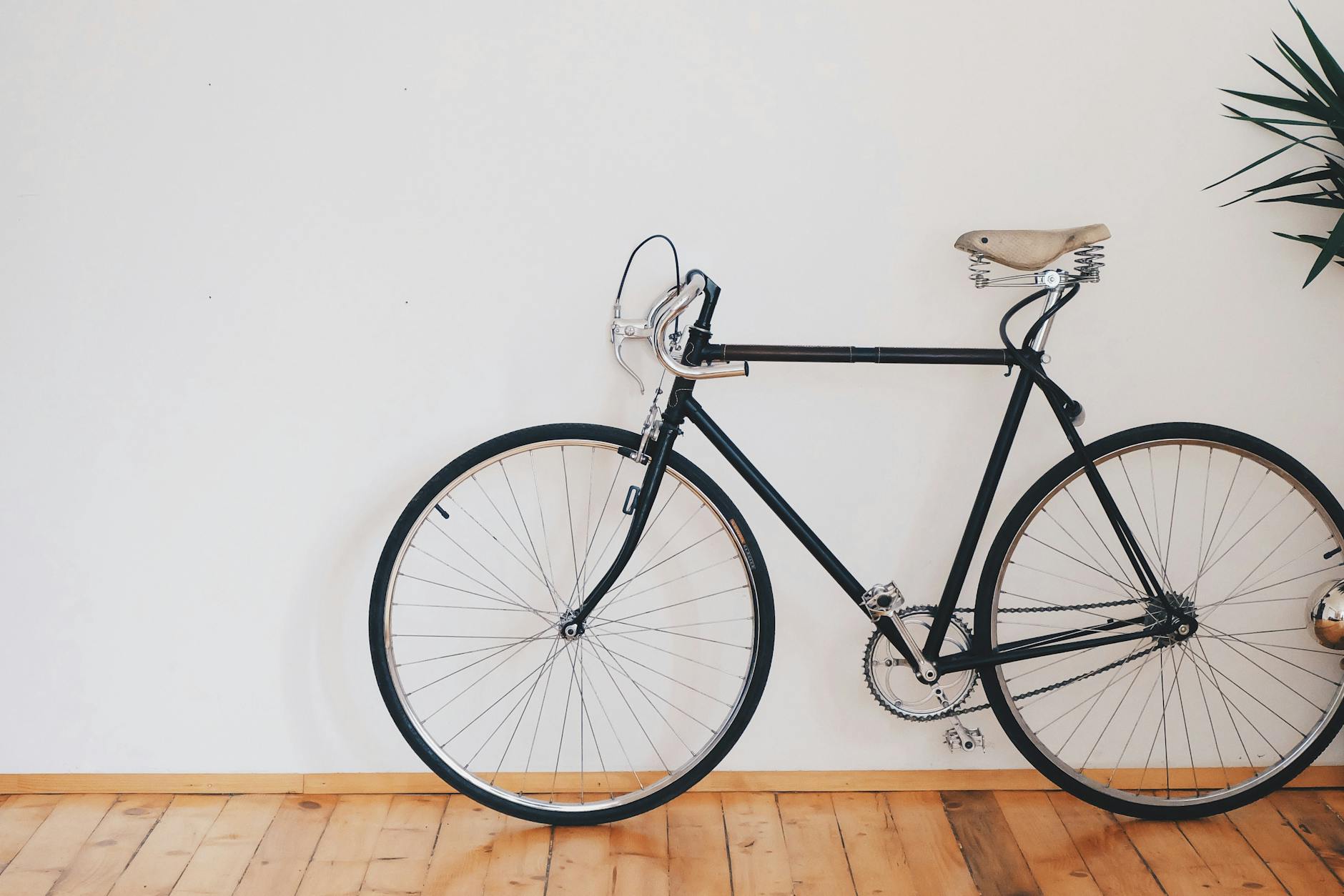
- The Maytag Gas Range with Speed Cook Microwave was awarded the “2023 Kitchen Innovation Award” for its exceptional design and functionality.
- It is available in multiple color options to match your kitchen décor.
- The Speed Cook Microwave function reduces cooking time by up to 50% compared to traditional microwave ovens.
Installation and Usage Guide for Maytag Gas Range with Speed Cook Microwave
Follow these steps to install and use your Maytag Gas Range with Speed Cook Microwave:
- Hire a licensed gas technician to install the appliance.
- Connect the gas supply to the range.
- Read the user manual thoroughly before operating the appliance.
- Place food in the microwave and select the appropriate cooking setting.
- Use the gas burners to cook on the cooktop.
What if the Maytag Gas Range with Speed Cook Microwave Malfunctions?
In case of any malfunctions, follow these troubleshooting tips:
- Check if the gas supply is turned on.
- Inspect the microwave door for proper closure.
- Reset the appliance by unplugging it for 30 seconds and then plugging it back in.
- Contact Maytag customer support for further assistance.
Listicle: Benefits of Maytag Gas Range with Speed Cook Microwave
Here’s a listicle of the advantages